Week 17: Project Development and System Integration
Breathing Library Swasa System Integration
Project Description:
The Breathing Library - Swasa project integrates sustainable and multifunctional features into a library setting. It includes air purification, CO2 removal, a relaxing reading light, and a community reading spot, along with advanced manufacturing techniques such as 3D printing, CNC machining, and electronics production.
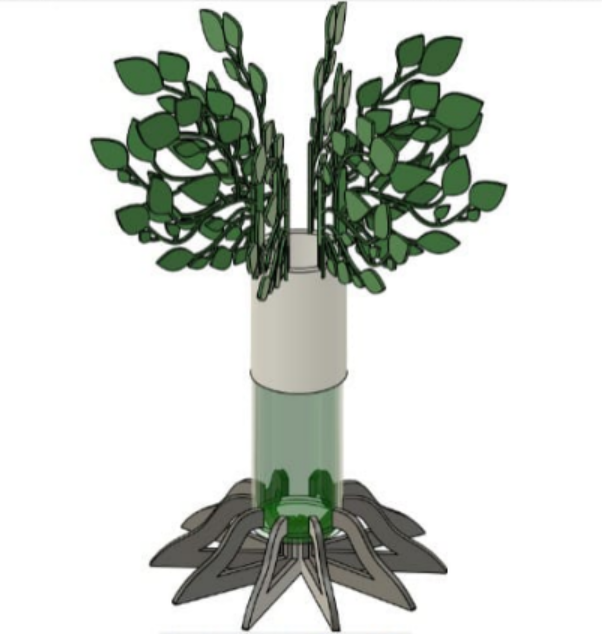
Features of Breathing Library Swasa:
- Automated Air Purification: Efficient air purification system to enhance indoor air quality.
- CO2 Removal: Uses algae to remove CO2 from the air.
- User-Friendly Interface: Easy-to-use interface for monitoring and controlling the system.
- Cost-Effective: Designed to be affordable with a focus on using locally sourced and sustainable materials.
- Customizable: Can be tailored to fit various library sizes and needs.
- Efficient Mechanisms: Mechanisms designed for optimal performance and energy efficiency.
- Adaptability: Adaptable to different environments and requirements.
- Easy Assembly and Maintenance: Designed for straightforward assembly and minimal maintenance.
- Future Expandability: Modular design allows for future upgrades and enhancements.
What tasks have been completed?
- Conceptualization and initial design of the Breathing Library - Swasa project.
- Creation of 3D models and 2D designs for components using CAD software.
- Procurement of materials and electronic components from specified sources.
- 3D printing of custom parts and housing.
- CNC machining and laser cutting of structural components.
- Designing and manufacturing printed circuit boards (PCBs).
- Soldering and assembling electronic components.
- Programming the microcontroller for system control and integration.
- Initial testing of individual components and subsystems.
What tasks remain?
- Final integration of all subsystems (air purifier, CO2 removal, reading light, etc.).
- Comprehensive testing of the integrated system to ensure functionality.
- Development of the user-friendly interface for monitoring and control.
- Further refinement and optimization of the system based on test results.
- Documentation of the final project and creation of dissemination materials.
- Conducting pilot implementation in a local library and gathering feedback.
- Making any necessary adjustments based on pilot feedback.
What has worked? What hasn’t?
What has worked?
- Successful design and 3D printing of custom parts and housing.
- Effective CNC machining and laser cutting of structural components.
- Accurate design and manufacturing of PCBs.
- Proper assembly and soldering of electronic components.
- Initial testing of individual components showed positive results.
What hasn’t worked?
- Some initial designs required modifications due to fabrication constraints.
- Integration of subsystems presented unexpected challenges.
- Some electronic components had compatibility issues that needed resolution.
What questions need to be resolved?
- How can the integration of subsystems be optimized for better performance?
- What is the most effective way to implement the user-friendly interface?
- How can the air purification and CO2 removal processes be further optimized?
- What additional features can be included to enhance user experience?
What will happen when?
- Final integration of subsystems and comprehensive testing.
- Development and implementation of the user-friendly interface.
- Pilot implementation in a local library and gathering feedback.
- Refinement based on feedback and further dissemination efforts.
What have you learned?
- The importance of detailed planning and design in project development.
- Challenges and solutions in integrating multiple subsystems into a cohesive unit.
- Effective use of advanced manufacturing techniques like 3D printing and CNC machining.
- Skills in electronics design, PCB manufacturing, and embedded programming.
- The value of iterative testing and refinement to achieve optimal results.
Production Methods:
- Laser Cutting: For precise cutting of acrylic and wood components.
- 3D Printing: For creating custom parts and housing.
- Circuit Designing: Creating electronic circuit layouts.
- PCB Milling: Manufacturing printed circuit boards.
- Soldering and Assembling: Integrating electronic components.
- Embedded Programming: Programming the microcontroller to control the system.
Sourcing Table:
Material/Component | Source | Example Suppliers |
Filament for 3D Printing | Fab Inventory | Fablab |
Wood Sheets | Fab Inventory | Fablab |
Acrylic Sheets, Cardboard | Fab Inventory | Fablab |
Electronic Components | Electronics stores, online platforms, Fab Inventory | Thomson Electronics, Amazon, Fablab |
Algal Growth Materials | Amazon | Amazon |
Beaker | King’s Aquarium | King’s Aquarium |
Aerator pump | King’s Aquarium | King’s Aquarium |
Electronics BOM:
Reference | Value | Datasheet | Footprint | Qty |
C1 | CP_Elec_D6.3mm_H6.1mm | https://api.pim.na.industrial.panasonic.com/file_stream/main/fileversion/19782 | fab:CP_Elec_D6.3mm_H6.1mm | 1 |
J1,J4 | Conn_PinSocket_1x03_P2.54mm_Vertical_SMD | ~ | -- mixed values -- | 2 |
J2,J3 | Conn_PinSocket_1x04_P2.54mm_Vertical_SMD | https://media.digikey.com/pdf/Data%20Sheets/Sullins%20PDFs/NPxCxx1KFXx-RC%2010487-D.pdf | fab:PinSocket_1x04_P2.54mm_Vertical_SMD | 2 |
J5 | Screw_Terminal_01x03_P3.5mm | www.on-shore.com/wp-content/uploads/ED555XDS.pdf | fab:TerminalBlock_OnShore_1x03_P3.50mm_Horizontal | 1 |
J6 | Screw_Terminal_01x02_P5mm | https://www.on-shore.com/wp-content/uploads/OSTTAXX0161.pdf | fab:TerminalBlock_OnShore_1x02_P5.00mm_Horizontal | 1 |
M1 | Module_XIAO-ESP32C3 | https://wiki.seeedstudio.com/XIAO_ESP32C3_Getting_Started/ | fab:SeeedStudio_XIAO_ESP32C3 | 1 |
LED | Neopixel String Lights | 1 (41 units) | ||
S1 | MQ 135 | 1 | ||
S2 | DHT Sensor | 1 | ||
Power Module | Adapter | 1 |
Material and Machining BOM:
SL NO | PART NAME | SOURCE | QUANTITY | PRICE | TOTAL |
1 | 3D PRINTING | FABLAB INVENTORY | 18 hrs | ₹200 | ₹3600 |
2 | M3 NUTS AND BOLTS | FABLAB INVENTORY | 15 | ₹5 | ₹125 |
3 | M4 NUTS AND BOLTS | FABLAB INVENTORY | 5 | ₹5 | ₹25 |
4 | PCB MILLING | FABLAB INVENTORY | .5 hrs | ₹150 | ₹75 |
5 | Card Board | Fablab | 1 | ₹.5 | ₹10 |
6 | Aquarium Cost (beaker) | Fablab | 2 | 300 | 600 |
TOTAL | ₹4435 |
Total Project Cost:
Electronics BOM Total:
₹2000
Material and Machining BOM Total:
₹4435
Overall Total:
₹6435 INR
Gantt Chart
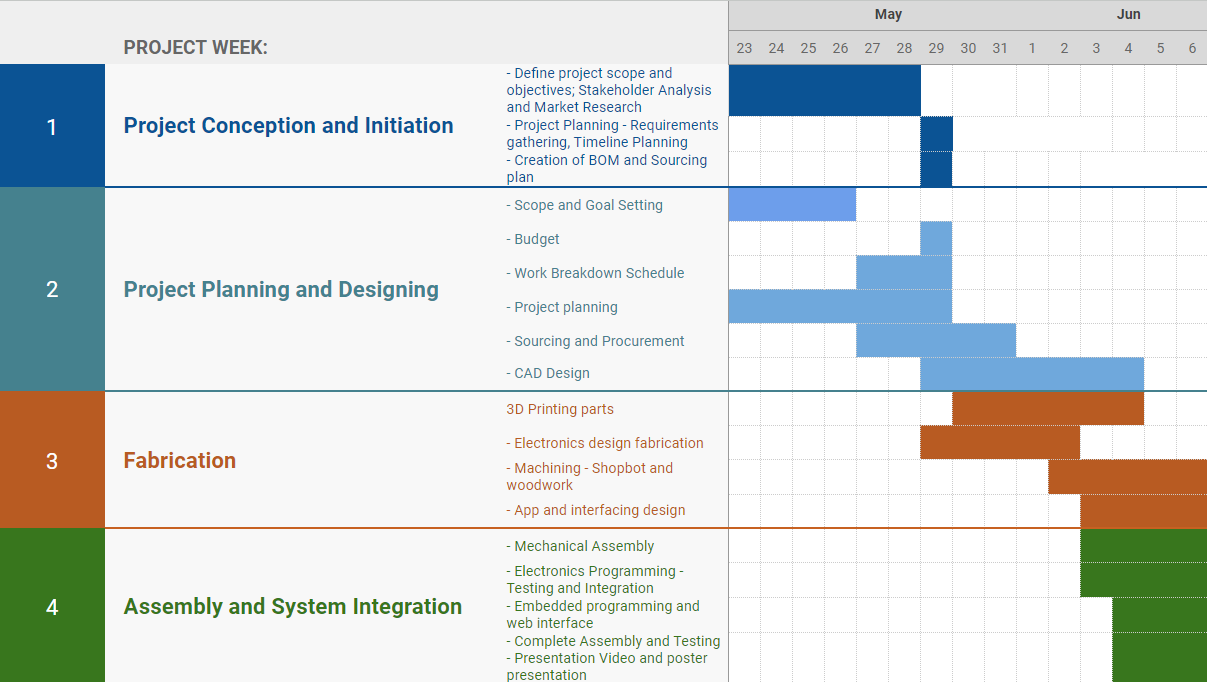